There are a variety of ways to quench materials, each with its own tradeoffs. This article will take an in-depth look at everything you need to know in determining whether you should quenching in water vs. oil.
What is Quenching Used For?
Quenching in oil or water is a heat treatment process for metals. Specifically, it focuses on the rapid cooling of a metal to alter the mechanical properties from one solid phase to another solid phase. One example is transitioning from the austenite phase to the martensite phase to increase the hardness of steel for applications such as swords, knives, and other tools.
For further reading on the process, check out what happens in a quench.
Should I Quench in Oil or Water?
Here is a high-level comparison table for quenching in oil vs. water.
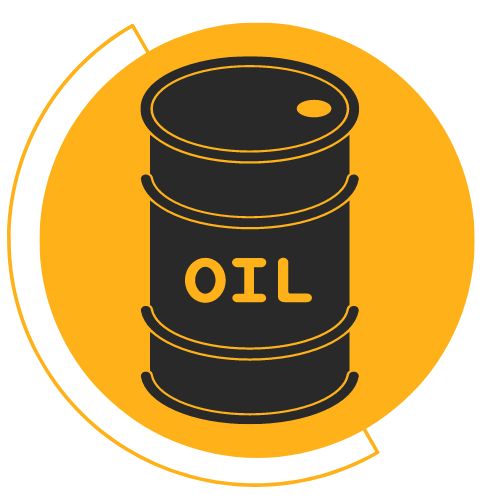
- Quench Speed: Medium-Slow
- Material Properties: Moderate Hardness, with Lesser Stress
- Applications: Odd Shapes or Variable Sections
- Flexibility: High
- Cost: Medium-High
Choosing whether you are quenching in oil vs. water is ultimately decided by your desired material outcome. Quenching with water is a much faster and cheaper process, but typically results in a brittle end product. Quenching with oil tends to be a bit slower, but results in a product with moderate hardness and less stress (typically the more desirable outcome).
It is worth noting that choosing between the two is highly dependent on the type of material. For example, some materials can only be hardened with water because oil quenching would cause irreversible damage to the product.
For a video comparison of quenching in oil vs. water, check out this video. Note how brittle the metal gets after quenching in water!
Quenching in Water
The most obvious advantage of water quenching is that it is faster than the air and oil quenching processes, less costly, and less time-consuming. In this quenching process, the heated material gets rapidly cooled, and you get an end product rather quickly.
The rapid cool speed generally impacts the end product by making it stiff and easily breakable. Depending on your desired outcome, this can be viewed as a pro or a con.
A key advantage of water quenching is that it is not flammable like its oil counterpart. There is also very little cleanup required when quenching with water.
Types of Water for Quenching
Water quenching is generally with 100% water, but brine (water and salt) is also a common quench technique. Both are much easier to control and less dangerous when compared to oil.
- Water – Heated material is cooled in tap or distilled water.
- Brine – Heated material is cooled in a mixture of salt and water.
Quenching in Oil
Oil quenching is the preferred choice in the metal industry. While material dependent, it generally results in more favorable material properties if the final product. This is because the process of hardening metal alloys with quench oil gives them the hardening and power needed without causing the end product to get stiff and brittle.
Quench oil heats up much slower than other liquids, such as water, and therefore cools down slowly as well. Effectively, this property ensures that the heated material has more stability and hardening time. The fact they oil can be controlled means that it’s very versatile within the context of the metal-working industry.
It is used for use when deeper and more uniform hardening is required in steels having a small or wide variation in grain size, in steels lean in alloy content, in parts having variable sections or odd shapes, and in steels having variable hardenability.
Types of Oil for Quenching
While there are many different types of oils that can be utilized in the quenching process.
- Specialized quenching oil – These oils are produced for the sole purpose of quenching. Commercial manufacturers, such as Fusion Chemical, have a variety of quench oils for various desired materials and quenching speeds. Typically knife makers prefer this type of quench oil since it can handle odd shapes and variations in grain size.
- Engine oil – Certainly an alternate use for this oil, but it tends to work relatively well from a quench performance perspective. One cool part is that you can use both new and used engine oil for quenching.
- Food-grade oil – The best part about food-grade oil is that it is relatively inexpensive and generally environmentally friendly. Vegetable oil is generally considered the best food-grade oil due to its ease of increasing toughness, hardness, yield strength, and elongation. Olive oil works well too if your goal is to deliver lower hardness but higher toughness.
Cool Rate by Quench Media
Each has its own tradeoffs, but each medium’s standard comparison method is the quenching rate. Brine is by far the fastest, with air by far the slowest.
- Oil – Heated material is cooled in oil (quench oil, motor oil, or cooking oil).
- Water – Heated material is cooled in tap or distilled water.
- Air – Heated material is cooled at standard room temperature.
- Brine – Heated material is cooled in a mixture of salt and water.
Conclusion
Since it’s one of the most critical parts of the metalworking process, using the right quenching process for heat-treating a metal is exceedingly important. It helps the metal achieve the desired properties (hardness, strength, elongation, or toughness) and therefore must be done thoughtfully.
For a comparison of quenching in oil vs. water, generally oil is the preferred medium. Both hobbyists and industrial companies find that specialized quenching oil has the preferred quenching properties and the most reliable product outcomes. It does come with a cost, but it seems to be well worth it.
No quench process is perfect, which is why it’s important for you to do your research. There is a wide spectrum of quench options for just about any purpose!